加工図面でも板金図面でも図面を書くときに気を付けておきたいことは、基準面を意識するという作業です。基準面を意識して寸法を引いた部品図と基準面を無視して寸法を引いた部品図とでは、部品の仕上がりが全く異なってしまうのです。同じ部品形状を示す寸法なのにどうしてこういったことになってしまうのでしょう?今回はその違いについて詳しく解説していきます。図面を書くときの基本となりますので、基準面を意識するということをしっかり理解しておきたいですね。
目次
長さ100mm±0という加工はできないという現実
部品を製作するときには、加工部品にせよ板金部品にせよ”公差”というものが存在します。これは、長さ100mm±0という加工が不可能だからです。もう知っていますよね。寸法±0という加工ができないことが前提としてあり、”公差”という概念が生まれているのです。 公差とは、所望する寸法に対する加工誤差を意味し、加工方法によって公差幅が違ってきます。例えば、研磨加工であれば公差幅は数ミクロンオーダーで仕上がりますし、切削加工であれば、数ミクロン~数十ミクロンオーダーで仕上がります。板金加工であれば、±0.5mmほどで仕上がりますし、溶接部品であれば、数ミリ単位で仕上がります。このように加工方法によって生じる誤差の幅が異なるのです。 ですが、世の中には、ナノオーダー(ミクロンのさらに1/1000)で仕上げることができる加工法もありますので、極力公差が0に近づけることができます。ですが、当然コストも跳ね上がりますので、一般的な部品を仕上げるために使う加工法としては選ばないかもしれません。 話を元に戻すと、部品を製作(加工)するときには加工誤差が必ず生じるということは、寸法を入れれば必ず誤差が生じるということを意味するのです。さらに言えば、寸法をつなげればつなげるほど、加工誤差は累積されることになるのです(※必ずしも比例的に蓄積されるとは限りません)。このような背景があることを理解した上で、基準面が持つ意味と役割について解説します。
基準面を意識した図面と意識しない図面の違い
では先ほどの加工誤差を踏まえて、基準面を意識した図面とそうでない図面の違いについて解説していきます。 その前に図面には一般公差というものが存在することをご存知でしょうか。当然設計者であれば知っていて当然なので、ここでは細かな解説は割愛しますが、先ほどの加工誤差を定量的にした加工誤差の幅を意味します。一般公差は図枠の隅に書かれていることが多く、長さによって公差域が異なっています。 例えば、以下のような公差域があります。 寸法1~20の場合、公差は±0.1 寸法20~100の場合、公差は±0.2 寸法100~500の場合、公差は±0.3 寸法500~1000の場合、公差は±0.4 寸法1000~2000の場合、公差は±0.5 長さが長くなるにつれて、公差域もだんだんと広くなっています。ここで話を簡単にするために、プラス側の公差幅だけを考えます。この公差域を使って基準面の役割について解説していきます。 寸法1~20の場合、公差は+0.1 寸法20~100の場合、公差は+0.2 寸法100~500の場合、公差は+0.3 寸法500~1000の場合、公差は+0.4 寸法1000~2000の場合、公差は+0.5 例えば、長さ800mmの長尺の部品を製作するとします。長さ800mmを一本の寸法線で表現すれば、一般公差は+0.4となります。
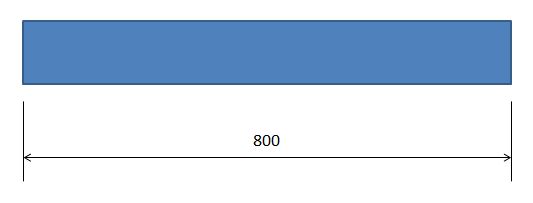
ただし、これは0~800までを一本の寸法で引いた場合の公差幅です。一方で、800mmを2本の寸法に分けたとします。(現実的にはこのような寸法の引き方をしないと思いますが、今回は例え話ですのでご了承ください(汗) すると、1本の寸法は0~400mmとなるわけですから、公差幅は+0.3となります。これが2本になると公差幅は+0.6となるわけです。
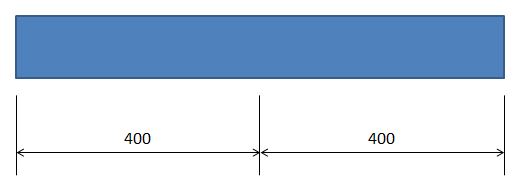
この寸法の引き方の意味は、1本目の寸法400mmに対しては最大400.3mmまでOKで、2本目の寸法400mmに対して最大400.3mmまでOKという意味です。ということは、最大で2本合わせて800.6mmまでOKという意味(部品図)になるのです。 同じ長さ800mmの長さの部品でも、寸法の引き方次第では、最大800.4mmにもなるし、800.6mmにもなるということです。寸法を累積するということは、加工誤差も累積するという意味なのです。こういった寸法の引き方がまさしく「基準面を意識しない寸法の入れ方」ということです。 ここで、「おいおい、0.4も0.6も変わらないじゃん!いちいち細かいんだよ(`Δ´)!」という声が聞こえてきそうですが、そういうことではなく、同じ800mmという寸法を表現するのでも、こういった違いがあるという意味を理解してほしいんです。では、2本に分けた寸法を誤差を累積させずに表現するにはどうしたらいいのでしょうか?その答えが”基準面”という考え方になります。 長さ800の片方の面を基準面とし、そこを基準に寸法線を引くことで加工誤差の累積が解消されるのです。
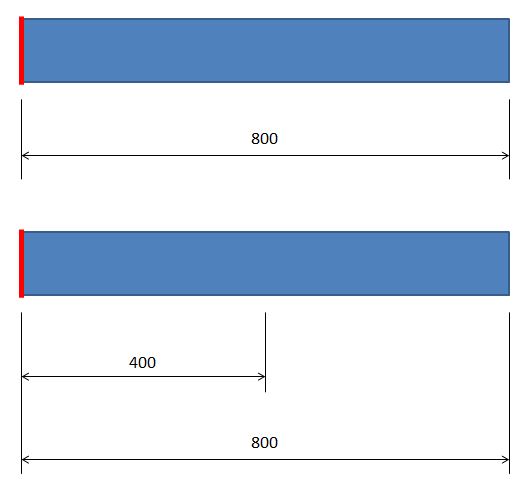
上図のように、基準面(左端にある赤の太線)から寸法を引いた場合、同じ2本の寸法線でも誤差の累積はなく、長さから生じる誤差だけになることがお分かりいただけるでしょうか?これで400mmの寸法誤差の影響を受けないことになります。 この考え方は、特に加工図面を書くときに必要となる考え方です。なぜなら加工部品を製作するときは、素材に対して1面加工面を作り基準面とするからです。まずはじめに加工者が行うことは基準面を仕上げることからはじまるのです。仕上げた基準面をもとに部品形状を切削加工していくのです。 簡単ですが以上が、基準面を意識した図面と意識しない図面の違いとなります。
基準面を決めて寸法を引く理由
この原理を理解すると、図面作成で寸法の引き方が見えてくると思います。部品の形状を表現するためだけに寸法を入れていくのではなく、誤差を極力抑えたい寸法の入れ方が自然と身に付くはずです。 もう少し具体的な例をいうと、穴位置を示す寸法が右から入れる寸法と左から入れる寸法とでは、全く仕上がりが異なるという例を紹介します。
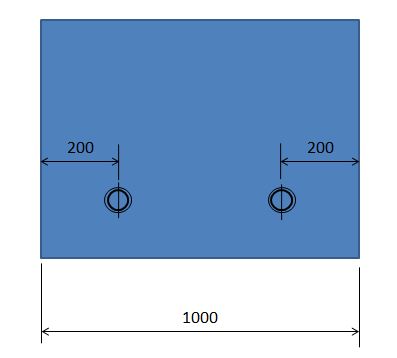
上図の例では、1000mm幅の板に右から200mmのところにタップがあり、左から200mmのところにタップがあります。通常タップは部品を取り付けるための役割なので、穴位置芯間が重要となりますが、もし、寸法の入れ方が右からと左からで分けてしまうと、加工誤差は大きくなることがわかりますでしょうか? 一般公差の場合だと、左の穴位置は、200mmなので、200±0.3mmの位置にタップがあります。ここでは、199.7の位置とします。一方、右側の穴位置は、1000mmの幅の誤差、1000±0.4からさらに200mmの位置となるので、200±0.3の位置となるのです。 最悪、1000mmの板材寸法が1000.4mmとなり、そこから200のタップ位置がマイナス目になったとすると、199.7の位置にタップが立つことになります。つまり、左側の端からは、800.7にタップが立つことなるので、タップ芯間としては199.7~800.7となり、601となるわけです。単純に600mmの芯間が1mmもズレた位置になってしまうわけです。
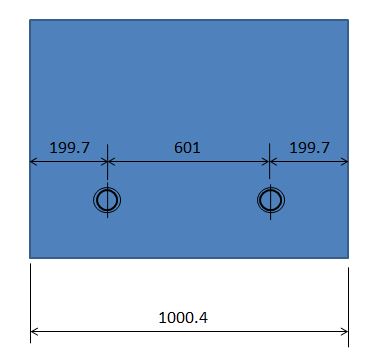
一方、タップ芯間に直接寸法を入れると、一般公差で600±0.4になるので、累積誤差が少なくなることがお分かりいただけると思います。
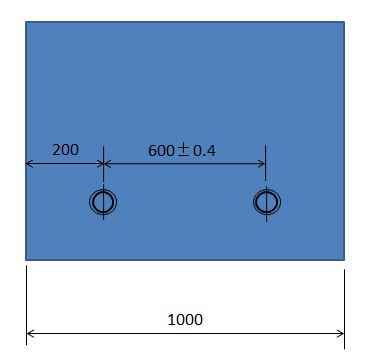
今回の例は、最悪の状態で仕上がった場合を示しましたが、この寸法で仕上がっても図面指示どおりなので加工業者に文句は言えないということです。 図面を作成するときは、こういったことを頭に入れながら寸法を引くことが大切になります。ただ、寸法を入れれば良いのではなく、ちゃんと部品製作のことを考慮して、必要に応じて基準面を意識すると、組立で不具合の起きない設計になることにつながります。
基準面の役割はもう一つある
基準面を決めることは、累積誤差を少なくすること以外にもう1つあります。それは、図面自体を見やすく統一性のあるものに仕上げることができるという役割です。 例えば、以下の2つの図面を見比べてください。
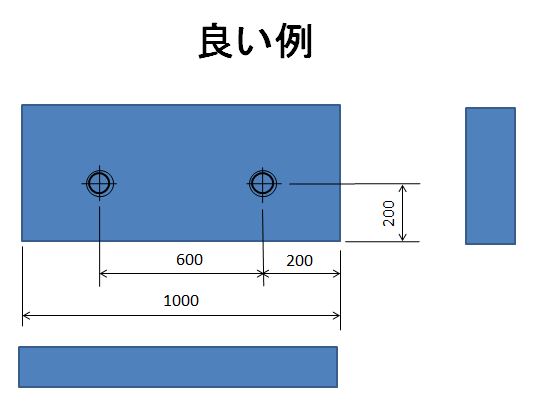
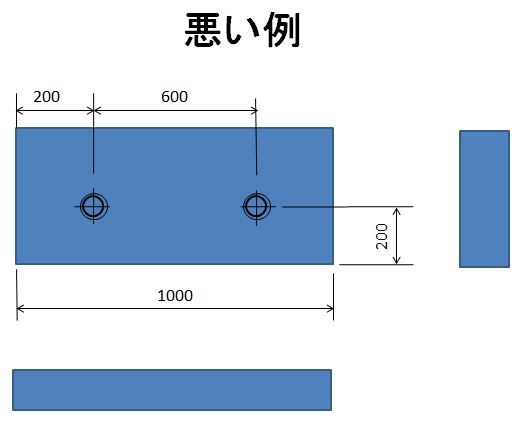
これは同じ形状のものを基準面を意識して寸法入れした図面とそうでない図面を比較したものです。良い例では図面は基準面を意識して書いたもので、悪い例は意識しない図面です。見比べてみてどうでしょうか?どちらが見やすいと思ったでしょうか? 板金部品の図面は加工部品と異なり加工基準面がありませんので、そういった意味では、基準面を設ける必要はないかもしれません。ですが、寸法の引き方として大事な面を決めて寸法入れすれば、図面として見やすいものになります。 2次元の図面では、3次元形状を表現するために三角法を用いますが、三角法で投影した配置は特に図面表記したい大事な面を配置するケースがほとんどです。ということは、この大事な面を基準面の役割として寸法を引いていくことで、図面に統一感を持たせ、より見やすい図面とすることができるのです。 三角法で配置した図の中で最も多く映し出されている線を基準面として、そこを基準に寸法を引いていくというやり方になります。 こういった寸法の引き方は加工部品のみならず、板金部品やその他すべての作図法として取り入れることができますので、見やすい図面作成に役立つ知識として取り入れてみてはいかがでしょうか?
コメント